Professional Recommendations on What is Porosity in Welding and Just How to Resolve It
Professional Recommendations on What is Porosity in Welding and Just How to Resolve It
Blog Article
Porosity in Welding: Identifying Common Issues and Implementing Finest Practices for Avoidance
Porosity in welding is a pervasive concern that typically goes undetected until it creates significant issues with the honesty of welds. This common issue can compromise the stamina and durability of welded frameworks, posing security threats and leading to pricey rework. By understanding the source of porosity and executing efficient avoidance methods, welders can substantially improve the quality and integrity of their welds. In this discussion, we will explore the essential factors adding to porosity development, analyze its detrimental impacts on weld performance, and go over the most effective practices that can be adopted to reduce porosity incident in welding procedures.
Typical Causes of Porosity
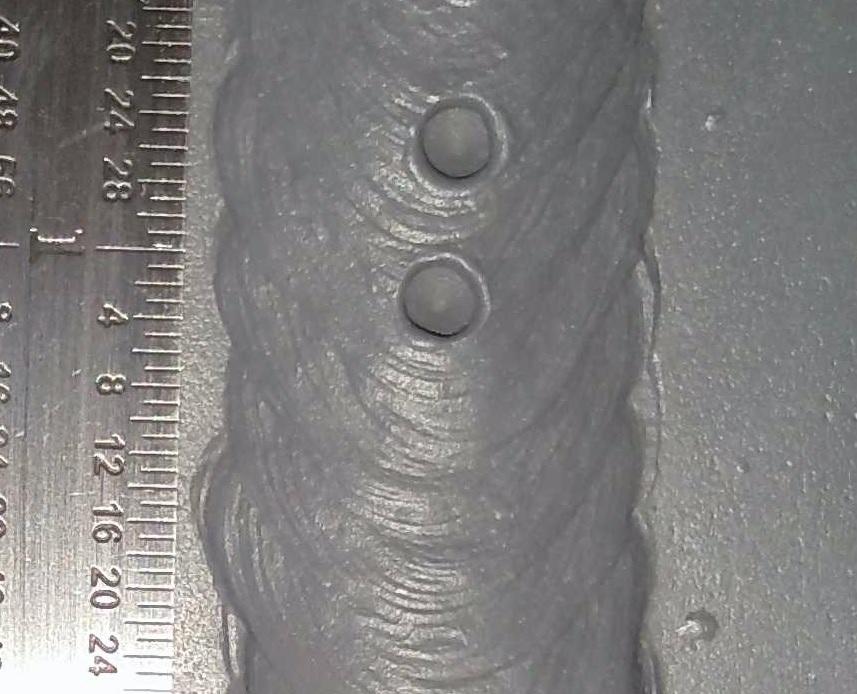
One more constant offender behind porosity is the existence of impurities on the surface of the base steel, such as oil, oil, or rust. When these pollutants are not properly removed before welding, they can evaporate and come to be trapped in the weld, triggering issues. Furthermore, utilizing unclean or damp filler products can introduce pollutants right into the weld, adding to porosity issues. To alleviate these typical sources of porosity, thorough cleaning of base metals, proper shielding gas choice, and adherence to ideal welding specifications are crucial techniques in attaining top quality, porosity-free welds.
Influence of Porosity on Weld High Quality

The existence of porosity in welding can substantially jeopardize the structural honesty and mechanical buildings of bonded joints. Porosity creates voids within the weld steel, deteriorating its overall toughness and load-bearing capability. These spaces act as stress and anxiety focus points, making the weld extra prone to breaking and failing under applied loads. Furthermore, porosity can decrease the weld's resistance to deterioration and other ecological aspects, further lessening its durability and efficiency.
One of the main consequences of porosity is a reduction in the weld's ductility and sturdiness. Welds with high porosity levels have a tendency to exhibit lower effect toughness and decreased capacity to flaw plastically before fracturing. This can be especially worrying in look at here applications where the welded components go through vibrant or cyclic loading conditions. Porosity can hamper the weld's capacity to properly transmit forces, leading to premature weld failure and potential security dangers in important frameworks. What is Porosity.
Finest Practices for Porosity Prevention
To enhance the structural integrity and top quality of bonded joints, what certain procedures can be carried out to reduce the occurrence of porosity during the welding procedure? Porosity avoidance in welding is important to guarantee the integrity and toughness of the last weld. One efficient practice appertains cleaning of the base steel, eliminating any type of contaminants such as corrosion, oil, paint, or wetness that could bring about gas entrapment. Making certain that the welding devices is in excellent condition, with tidy consumables and proper gas flow prices, can likewise significantly lower porosity. Furthermore, maintaining a steady arc and controlling the welding criteria, such as voltage, current, and take a trip speed, aids create a regular weld pool that decreases the danger of gas entrapment. Making use of the appropriate welding strategy for the certain product being welded, such as readjusting the welding angle and gun setting, can further stop porosity. Regular assessment of welds and prompt remediation of any kind of issues determined throughout the welding process are necessary techniques to avoid porosity and generate top quality welds.
Significance of Appropriate Welding Methods
Applying appropriate welding techniques is vital in guaranteeing the architectural stability and top quality of welded joints, constructing upon the foundation of reliable porosity prevention actions. Excessive warmth can lead to enhanced porosity due to the entrapment of gases in the weld swimming pool. Additionally, utilizing the appropriate welding specifications, such as voltage, existing, and travel rate, is essential for accomplishing audio welds with very little porosity.
In addition, the choice of welding process, whether it be MIG, TIG, or stick top article welding, need to align with the certain needs of the project to make sure optimum results. Proper cleansing and prep work of the base steel, as well as choosing the ideal filler product, are also vital parts of proficient welding methods. By adhering to these finest techniques, welders can minimize the risk of porosity formation and create top notch, structurally audio welds.
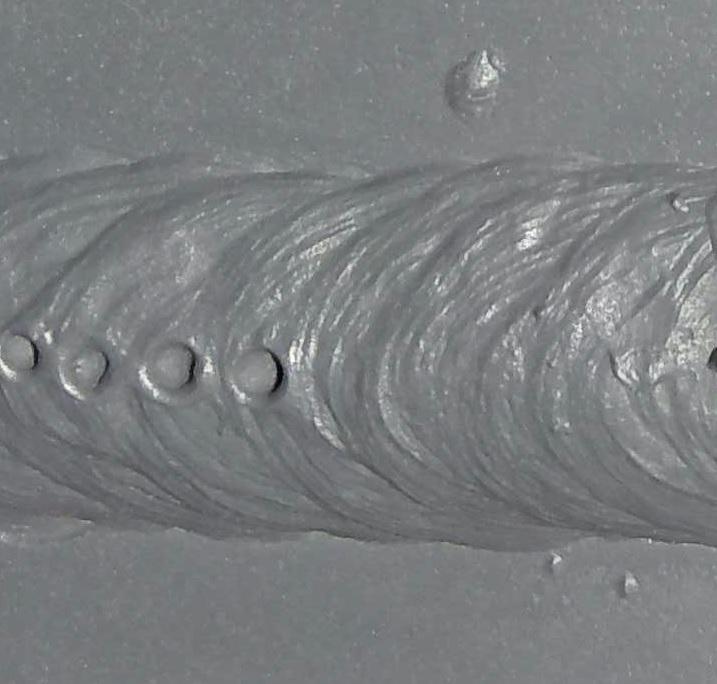
Evaluating and High Quality Control Procedures
Quality assurance procedures play a crucial duty in validating the honesty and integrity of bonded joints. Examining treatments are necessary to identify and protect against porosity in welding, making certain the toughness and longevity of the last product. Non-destructive testing methods such as ultrasonic screening, radiographic screening, and visual evaluation are commonly used to recognize prospective problems like porosity. These techniques permit the analysis of weld high quality without compromising the honesty of the joint. What is Porosity.
Post-weld get more examinations, on the various other hand, examine the final weld for any issues, including porosity, and validate that it satisfies defined requirements. Carrying out a thorough high quality control strategy that includes complete testing treatments and inspections is vital to reducing porosity issues and making sure the total top quality of welded joints.
Final Thought
To conclude, porosity in welding can be an usual concern that influences the quality of welds. By identifying the typical sources of porosity and carrying out ideal practices for prevention, such as appropriate welding methods and screening steps, welders can guarantee top quality and reliable welds. It is necessary to focus on prevention approaches to reduce the event of porosity and preserve the integrity of bonded structures.
Report this page